PROJECTS
"UDE"
Fall 2017
Ude, meaning "arm" in Japanese, utilizes an unconventional actuator to move the elbow joint. Instead of using standard motors, pneumatics, or linear actuators which require large power sources, Ude moves via a synthetic bicep made by integrating heat sensitive Nitinol wire in a tessellation origami design powered by six 9V batteries. The synthetic muscle is flexible and may be used to emulate a wide variety of other sized muscles. Future iterantions will utilize the same technology to actuate individual fingers, the wrist, and shoulder joints.



AQUAPONICS
Fall 2016
The aquaponics system is programmed through an Arduino and scheduled to activate the water and air pumps every hour. The Arduino is integrated with a Raspberry Pi touchscreen to display temperature and pH of the fish tank. The touchscreen can also be used to manually control the grow light, air and water pump if required. The system pulls water rich in nutrients from the fish's fecal matter. The water is purified by the plants and filtered back into the fish tank. The system was a collaborative effort between four members of the “team” in which I served as president. I was responsible for the woodworking aspects, electrical wiring, and creating the logo.
SCIOLY ROBOT ARM
2016-17
This robot arm was the third and final attempt used to compete in science Olympiad tournaments. The arm had to fit certain constraints such as fitting within a certain cramped volume. The robot specialized in picking up sacks of pennies in which it had to precisely dispense at a different locations. This project served as my epitome of my career as the head of building within the team and also won first place at regionals. I was responsible for the entirety of the physical construction, designing the minibot system, and wiring.


CAN CRUSHER
Spring 2015
The Can Crusher Master Project was assigned to all freshmen taking the engineering course. My team was the only one in the freshman class to produce an operating project. The can crusher runs autonomously after an initial start button is pushed. It stops automatically when it senses there are no more cans or if an emergency stop button is pushed overwriting all operations. I served as the President in this particular engineering group and was responsible for the wood working on the can holder and crushing mechanism, wiring electrical components, and programming the robot controller.
T-SHIRT CANNON
Fall 2017
As a reward for successfully attempting the FMS master project, we were allowed to build a t shirt cannon to be used in future football games. However, for safety purposes, the pressure of the cannon could not exceed 30 psi. We also had to use normal air as opposed to compressed CO2. The small air hose that fed into the cannon was at 30PSI however the volume of air being released at an instant was not enough to launch a t shirt very far. Our solution was a tank that slowly built up pressure at high volumes. Once a release valve was triggered the tank would decompress instantaneously releasing all the pressurized air out at a high volume launching the t-shirt. I was responsible for assembling the PVC and creating the mechanism as well as the black paint and vinyl stickers.

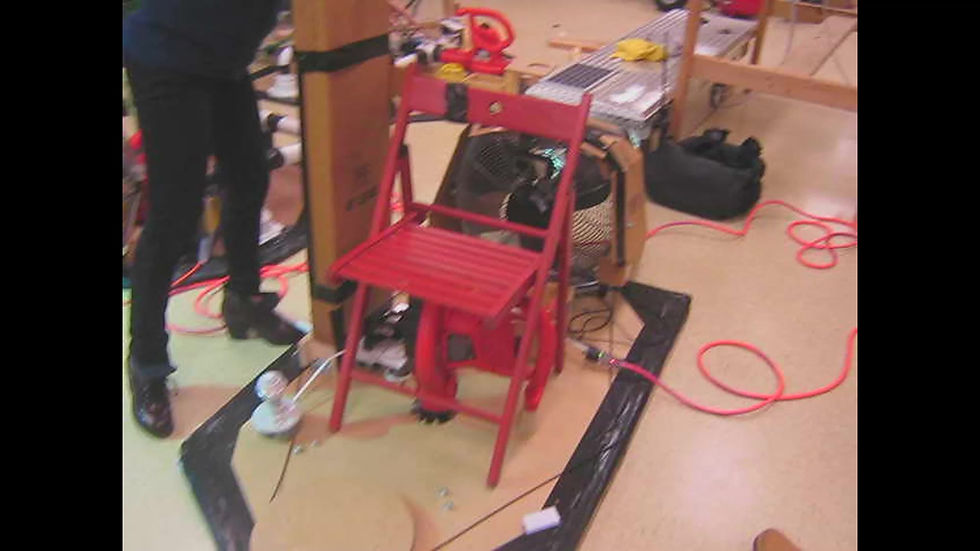

HOVERCRAFT
Fall 2015
The hovercraft masterproject was assigned to my "company" sophomore year. We had to construct a hovercraft that docked at the docking bay and picked up material. I was responsible for designing and building the air distribution system as we were only allowed one leaf blower as well as electrical fabrication.
AUTOMATED KEYCHAIN MAKER
(Flexible Manufacturing System)
Spring 2017
My second semester junior master project was the dreaded flexible manufacturing system. This was a project the engineering instructor only gave once every 4 years to the "most capable" team. The project required the integration of the robot arm, CNC mill, and an Arduino, all with different coding languages. The project required a piece of aluminium stock to be picked up, treated, and milled to make a finished key chain. The team was split and specialized in different fields Though separate aspects functions flawlessly, there was not enough time to successfully integrate everything into an autonomous system. I was responsible for programming the robot arm, and designing/building what we dubbed the dunker.
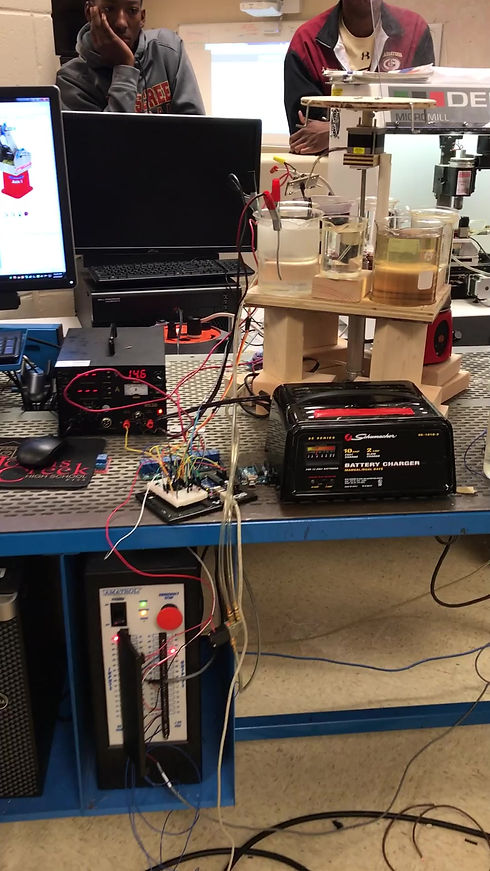
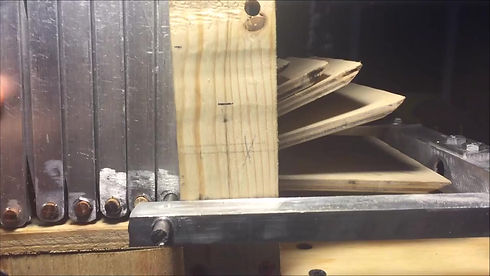
DRAWBRIDGE
Spring 2016
My sophomore year master project was to create the draw bridge, usually a junior year project. The team decided against a simple bascule bridge or swing bridge design in favor of an original design that challenged us technically. The bridge was named the scissor bridge as it resembled a scissor lift on its side. The bridge is actuated by a pneumatic cylinder controlled by the computer. I was responsible for both the metal and wood working aspects, including assembling the final product.

TOWERS
2016-17
Although on the surface it seems simple, this tower was constructed after extensive planning. After taking AP Physics and structural engineering, I used my knowledge in forces to calculate the optimum design too efficiently distribute 15 kilograms through out a .015 kg structure. The tower qualified for bonus points in design as well as holding all 15 kilograms securing a 1st place win at the Science Olympiad Regional Tournament.
